Production possibilities of Valenta ZT s.r.o.
Thread rolling
What is thread rolling?
Thread rolling is the cold forming of the surface area of circular cross-section components . The thread is created by means of the forming of the workpiece under the enormous force application of two rotating rolling tools, between which the component is placed. By the penetration of the section of the rolling tool into the surface of the workpiece, the material is cold-pressed up to the base of the thread rolling tool and rolled to the nominal dimension.
Advantages of thread rolling:
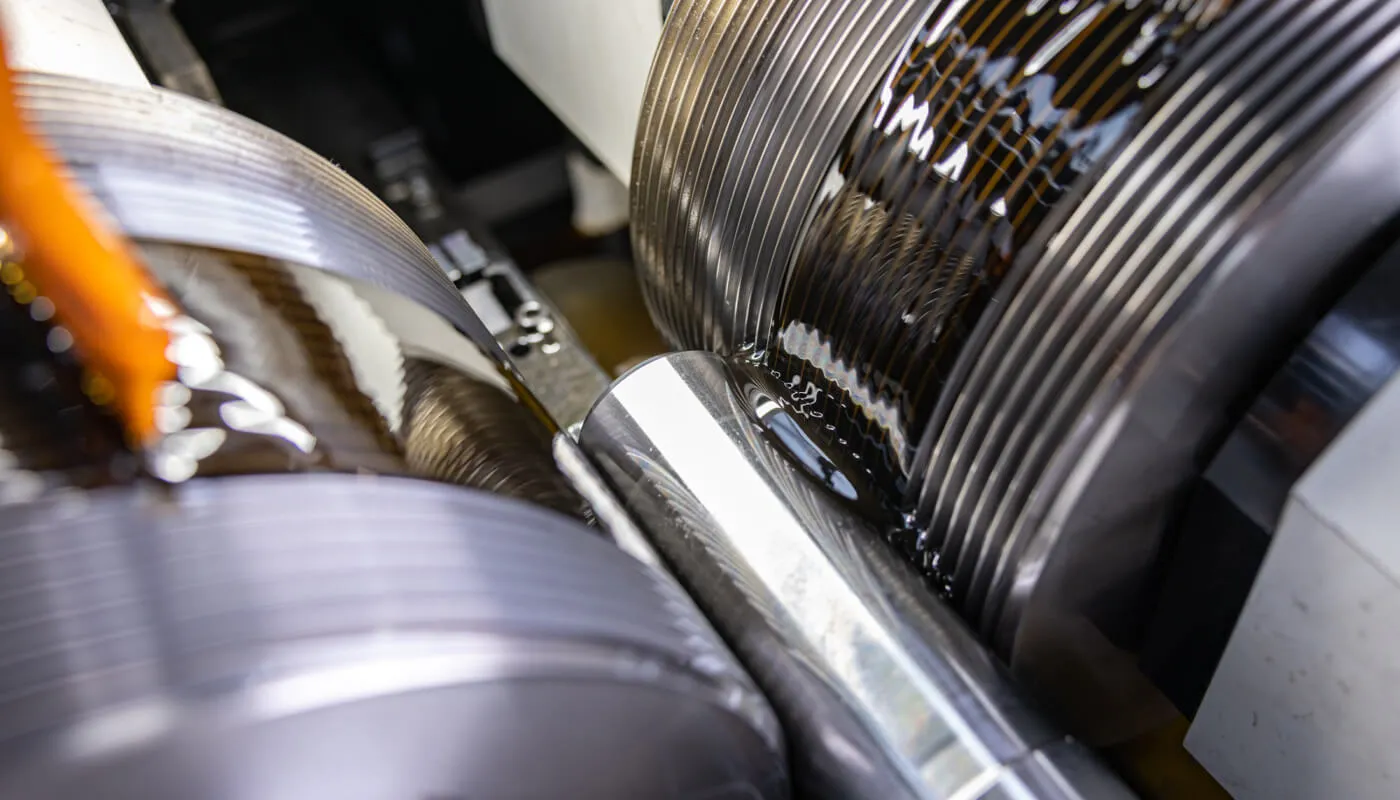
- Increase of strength by cold forming
- A rolled thread, in contrast to a cut thread, does not interrupt the course of the material's fibers
- The rolled thread has very good surface roughness values
- Notch sensitivity is also reduced
- Rolled threads are characterized by high dimensional accuracy
- Rational and fast production
- Rolled thread is cost-effective due to the productivity of production in large series
Production possibilities:
- Wide range of rolling tools (M, Tr, UN, UNC ...)
- Right-hand/left-hand variant
- Single/multi-thread
- Rolling of threads under hot-dip zinc
- For the rolling of threads of a length up to 6,000 mm
- Diameters up to 120 mm (depending on the material and type of thread)
- Several rolling machines of a wide range of the rolling force
Materials suitable for thread rolling:
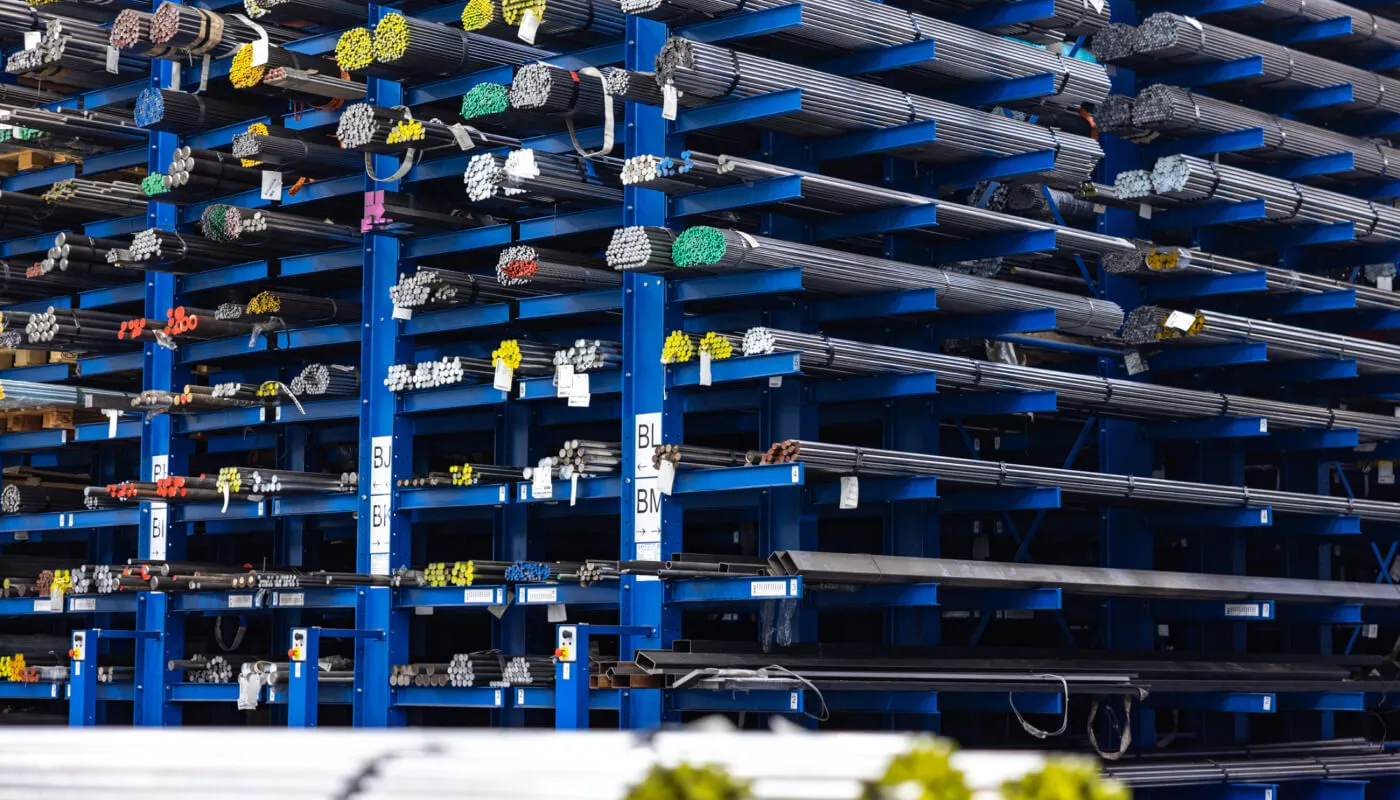
- All metallic materials having a ductility of at least 6% and tensile strength no more than 1,300 MPa (N/mm2)
- High-alloyed, corrosion-proof and heat-resistant steels
- Special aluminium alloys
- Brass in riveting quality and cooper alloys
- Special nickel alloys
- At hollow bodies and tubes the thread can only be rolled if the wall thickness is sufficient (these wall thickness values depend on the type and depth of the rolled section)
Nevhodné materiály pro válcování závitů:
- Křehké materiály jako Ms58, šedá litina apod.
- Měkké materiály jako olovo
- Plasty a jiné nekovové materiály
Machining of components/threads
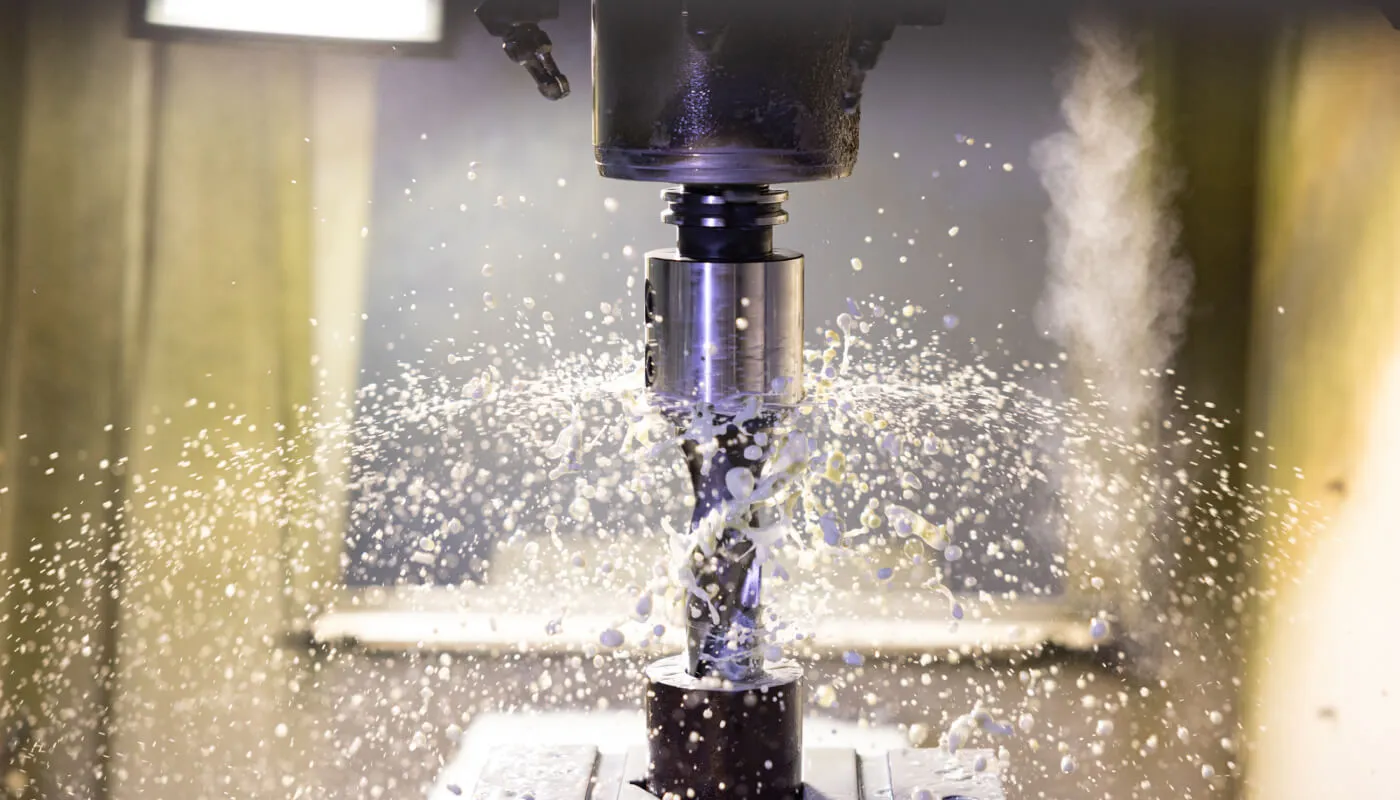
We own several working machines, which enable us to adapt flexibly to your requirements.
- Machining of large diameters, lengths
- Lathe-turned shafts and milling of shaped parts
- Preparation of input material for thread rolling
- Machining of nuts, washers etc.
U-bolt bending
We have our own U-bolt bending equipment. Cold and hot bending of various materials, dimensions and lengths. Possibility to bend also larger diameters and lengths.
Lettering on finished products
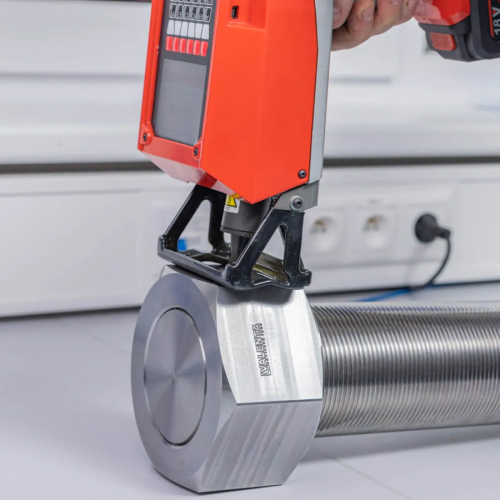
Upon your request we can mark all products from a custom production series with a text specified by you. The possibilities and limiting factors are determined by the type of the selected material, class, dimensions of the part, quantity etc.
Another option for labeling products is their labeling or packaging and subsequent sticking with our label, which only contains a description of the product. Of course, it is also possible to stick the package with a label that you supply to us in advance. Packaging and labeling options must always be consulted before production begins, if required.
Measuring and inspection of threads
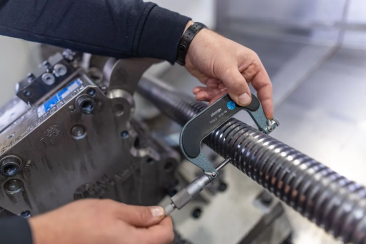
We pay attention to high quality both for stock and production items. We perform thread quality inspection by means of usual measuring tools and methods, the main ways include:
- Thread gauges for male and female threads - wide range of measuring for M, Tr and other threads, such as UNC, UN ...
- Three-wire method of thread measuring - for the verification of the thread mean diameter.
- Set of contacts and micrometer calliper gauges for threads for the quick check of correctness of the thread mean diameter.
For enquiries and technical questions please contact us in the REQUEST section, by e-mail or by phone, we will be happy to advise you.